ENGINEERING AND SOFTWARE
HVAC SOLUTION
I - AIR HANDLING UNITS (I-AHU)
A. PREMISE
I-AHU is a web solution for the design and selection of Air Handling Units. This web solution is the best you can choose because you can have the following main benefits:
​
-
Web software is accessible anywhere.
-
There is no update hassle.
-
You can run a web application no matter which OS you use.
-
All users of the application are using the same version, which means that there is no possible incompatibility.
-
No specific system requirements are needed which does not limit any customer, agent, or designer to use it anytime, anywhere.
-
No manual updates are necessary.
-
Web software is more cost-efficient.
-
The web application does not occupy disk space on the local computer.
-
Using a web software, you have full control of logins and you can approve access for each user.
-
You can receive statistics (see our paragraph BI) to follow your sales network and find strategy to improve the efficiency of your sellers or OEM.
-
You can share offer and selections filtering the access profiling the users.

B. BASIC VERSION (Selection and offer)
​
The IDEA AHU software allows the user to select, calculate and evaluate Air Handling Units (AHU) with several sections, all suitable components, in every condition.
​
The software is easy-to-use, quick, and intuitive, and is based on a large database of components that can be enlarged and integrated. For each kind of section there are already saved technical details of the component, the mounting rules to determine the dimensions and the number of pieces needed to build the AHU.
​
The application will be supplied in 2 basic languages (English and Italian), it’s possible to add other languages, and in that case, we need to receive the translation of all texts used by the program. For each new language there is a fee that is shown in paragraph PRICES.
​
The frontend is divided in sections. The user can navigate between the sections having the possibility to change some parameters and recalculate the AHU quickly using the new data.
​
-
Selection
Clicking on the selection option a user can define the following characteristics:
-
Unit specification
-
Standard
-
Kitchen
-
-
Installation site
-
Indoor
-
Outdoor
-
-
Casing material external
-
White-grey painted steel
-
Inox steel AISI 304
-
All other material used by the customer
-
-
Casing material internal
-
Zinc-coated sheet
-
Drilled zinc-coated sheet
-
All other material used by the customer
-
-
Profile name
-
P155/45 PS OX
-
P255/45 PS OX
-
All other profile used by the customer
-
-
Panel insulation
-
Expanded polyurethane
-
Rock wool
-
All other material used by the customer
-
-
Panel Thickness
The “Thermal performance”, “Thermal bridging” are related to the casing and profile and are defined in a database.
​
2. Params
Second step is the selection of the frontal dimensions of the AHU. The user has to insert:
-
Airflow
-
external static pressure
-
required air speed
The software gives back all the suitable dimensions to meet the requirements.
You have the following options:
-
Use dimensions referred to the standard production; the software will show 3 sizes closest to the requests.
-
Calculate optimal dimensions, fixing minimum ratio, Height/Width of frontal section and using required air speed and air flow.
-
Supply external dimensions; software will calculate air speed using required air flow.
In this section the user can also define kinds of unit:
-
Functionality, Supply and return;
-
Levels, 1 or 2;
In case of return air, the user has to define air flow, external static pressure and air speed also for this part of the unit.
3. Location
Third step is the selection of the project location. In this section the software uses a large database with the main locations in the world and gives back summer and winter design conditions from the ASHRAE 2017 Standard.
Using the internal temperature and relative humidity, percentage of external air the software calculates mixing air for summer and winter.
4. Schema
The last step to define the AHU is the schema. Here you can add, remove, and edit the component that you select for the units. The following components are available:
-
Plenum with 1, 2 or 3 dampers available in horizontal or vertical version, dampers are automatically selected from a database with standard dimensions using the request max velocity and the external air percentage set in the step 3 (location);
-
Frontal damper selected from a database of standard dimensions;
-
Pleated, wave, bag, absolute, carbon and fluidex (used for kitchen units) filter, all the filtration class are available; the software can automatically select the number of filters, finding the optimal solution in order to cover all internal available space, in alternative, a user can force the dimensions of the filter and the software calculates correct number of them.
-
Heating and cooling coils are calculated using our dll or dll by our customers; we can supply price, material part list and worker time for each activity involved in the production; we also supply a BIM drawing of the coils; we also can add dll from your supplier. The cooling coils are water cooled or DX (we have all the most popular refrigerant), the heating coils are water, condenser, and steam. All coils can be calculated in both modes (heating can be verified in cooling and viceversa). The dimensions of the coils are calculated considering the characteristics of the frame that you choose and the internal dimensions of the unit.
-
Cross flow and rotary heat recovery calculated using dll by Recuperator or by Eri.
-
Centrifugal and plug fans by Ziehl Abegg and our dll to simulate Nicotra, Comefri and EBM.
-
Humidifier steam, spray and contact; the humidification system can be selected according to the required efficiency.
-
Drop eliminator
-
Gas burner;
-
Sound attenuator.
-
Profiles to divide the units in boxes.
In this step you can also:
-
Watch the drawing with the main measures in any moment;
-
Have a fast datasheet preview; on datasheet it is possible to check all detailed technical specification of each section. Dimension and number of filters, pressure drops, capacities for coils, water and air pressure drops, power input for fan, efficiency, fan curves, etc.
-
Check the ERP report;
-
Check energetic class for summer and winter period;
-
Having a detailed price preview.
-
Save the offer in the database. The saved offer can be shared with:
-
other user that has permission to access. The permission can be defined as “only read” or “read/write” to allow the editing too;
-
Technical office connected with Inventor by AUTODESK.
-
A very interesting function was implemented to allow to the users to fix a target for energetic class or to find a solution ERP compliant optimizing the costs.
The best solution is obtained reducing the pressure drop and finding the heat recovery and the fans with the better efficiency. If it is not possible to reach the correct result working only on the components, the software will search the first size bigger than the current frontal section in order to reduce the air velocity. These operations, in complete automatically way, are done considering the minimum costs to reach the results.
C. CONNECTION TO INVENTOR
​
-
Executive drawing and production
I-AHU uses AUTODESK Inventor as standard, but we can migrate in any other 3D CAD software (solid Edge, Solid Works, etc.). The cost of the migration can be evaluated when we receive the specification.
Given that this is a web-based application, this characteristic allows automatical importing of all data from an offer made by a remote user directly to Inventor, avoiding any kind of transferring of files and import/export functions.
​
​
​
​
​
​
​
​
​
​
​
​
​
​
​
​
​
​
​
​
We created an add-in inside Inventor that allows importing data from an offer stored on cloud in order to automatically obtain:
​
-
a 3D models / assemblies for the end customer. In these models, the software generates the doors, the inspection windows and all the other parts such as profiles, corners, omega etc.;
​
​
​
​
​
​
​
​
​
​
​
​
​
​
​
​
​
-
for panels, the application generates precise 3D models that indicate the exact arrangement of the two metal plates that form the panel with the necessary workings and holes. Flat pattern / unfolded view needed for machining and drilling is generated for each sheet metal too;
​
​
​
​
​
​
​
​
​
​
​
​
-
the documentation for the production, particularly the 2D dimensional drawings of individual sheets with their workings as well as assembly drawing;
​
​
​
​
​
​
​
​
​
​
​
​
​
​
​
​
-
Bill of Material (BOM) in Excel fully adjustable to client requirements;​​​​
​
​
​
​
​
​
​
​
​
​
​
​
​
-
DXF files for CNC machining or printing, which guarantees a precise outcome, as well as PDF files;
​
​
​
​
​
​
​
​
​
​
​
​
​
​
​
​
​
-
All files saved in “Project Folder” specified by user
​
2. BIM
Using Inventor the technical office can create for a specific AHU stored on cloud the correspondent BIM file.
​
​
​
​
​
​
-
The BIM file, created in IFC format, includes all the information about the unit including:
-
Technical datasheet;
-
IOM manual;
-
Product life cycle;
-
Product disposal and recycling information;
-
Product certification (ARI, EUROVENT, SAFETY, CE, etc.).
This is full DYNAMIC HVAC BIM because it is connected to the server so any changing on the unit will be involved in the BIM file allowing a designer to quickly update his Revit MEP project.
As soon the BIM file is created it will be available immediately to the user of I-AHU that can download it just with by clicking on the frontend.
​​
​
​
​
​
​
​
D. ​QR Code
​For each unit the software will create a QR code to identify it and connect it to the information on server.
You can attach the QR code on the unit and read it, using a mobile, and have access to:
-
the technical datasheet;
-
IOM manual;
-
Service information (not included in this offer)
E. Refrigerant circuit
Our company have a long experience on the refrigerant circuit calculation. We have a database with 5’000 different compressors from Copeland, Bitzer, Frascold, Dorin, etc.
All the most popular refrigerant are in our system. We can propose an automatical selection of the compressors, evaporator and condenser using the dimensions and the capacity you need.
F. EUROVENT SERVICE
We offer an annual service to cover all the needs referred to the Eurovent certification, in particular we offer:
-
Support during the AUDIT;
-
Calibration of the data after the test;
-
Upgrading to the new Eurovent specification.
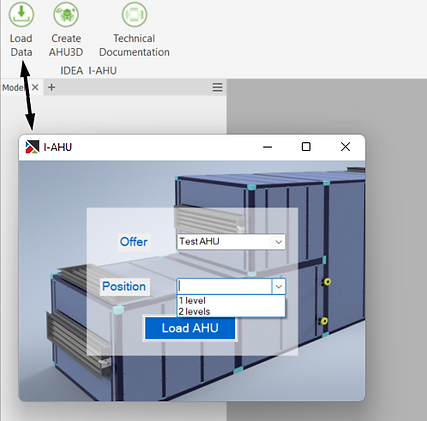




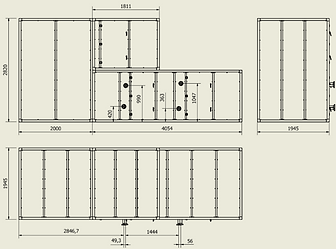
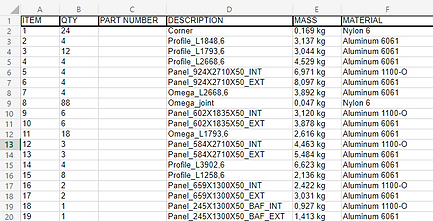
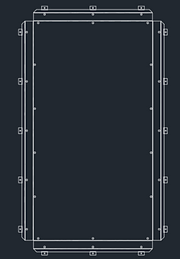




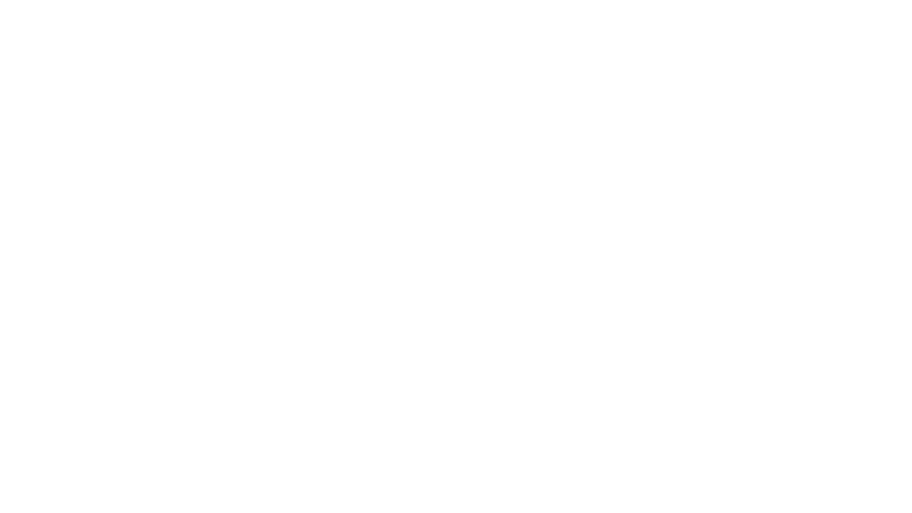